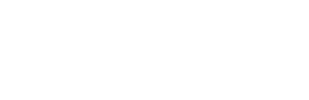
Job Information
Pactiv Evergreen Maintenance Reliability Manager in Plant City, Florida
Overview
Pactiv Evergreen Inc. (NASDAQ: PTVE)is a leading manufacturer and distributor of fresh foodservice and food merchandising products and fresh beverage cartons in North America and certain international markets. It supplies its products to a broad and diversified mix of companies, including full service restaurants and quick service restaurants, foodservice distributors, supermarkets, grocery and healthy eating retailers, other food stores, food and beverage producers, food packers and food processors. To learn more about the company, please go to the company website at pactivevergreen.com.
25 miles east of Tampa, Plant City is an incorporated city in Hillsborough County, Florida, approximately midway between Brandon and Lakeland along Interstate 4. The population was 34,721 at the 2010 census.
The Pactiv Evergreen Plant City Converting Facility is located in Plant City, Florida, less thanan hour outside Tampa and its amenities and beautiful beaches. Opened in 1992 and expanded in 1998 with 195 team members, the facility prints and die cuts refrigerated gable top cartons for a variety of global brands found in retail groceries throughout the US.
Responsibilities
Purpose of the job:
The Maintenance Reliability Manager is responsible for assisting with the development of reliability based maintenance strategy, based on preventative and predictive maintenance. This individual will work directly with the Maintenance Team Leader to build a reliable and effective CMMS system and maintenance team. The Maintenance Reliability Manager will work independently and with other plant personnel to perform preventative, predictive and routine maintenance tasks. All Store Room Attendants will report directly to the Maintenance Reliability Manager.
The Maintenance Reliability Manager makes a direct contribution to important plant goals of increasing labor productivity, reducing maintenance costs and improving equipment reliability. This is accomplished by preparing detailed job plans, coordinating key scheduling activities with other departments and ensuring work order data integrity. This person needs a complete understanding of the store room function, inventory management and parts distribution. The Maintenance Reliability Manager will have the primary authority and responsibility for overseeing the management of store room inventories, activity and ensuring inventory data integrity. This role serves as the central point of contact for all maintenance repair and operations (MRO) materials management system. This position is expected to lead and participate in plant level Continuous Improvement, Lean, Root Cause Analysis and Six Sigma projects when applicable.
Essential Functions/Responsibilities:
Demonstrate EAM proficiency utilizing the Materials Management and Maintenance modules of the CMMS
Run inventory cost modules to identify overstock and under stock conditions and adjust stock levels when necessary.
Generate and analyze key performance indicator reports (i.e. daily stock movement, due-in, past-due, monthly inventory accuracy, mean time between failure ect.)
Schedule, oversee and create cycle count documents
Convert work requests to work orders in CMMS/EAM system
Review and close out completed work orders
Update equipment history and other pertinentinformation
Continuously improve the preventative and predictive maintenance activities by utilizing key performance indicators as well as work order and customer feedback.
Approving and prioritizing new work order requests. Analyze work order feedback.
Ensure accuracy of the information on the new work requests before the request is converted to a work order
Use historical data to estimate labor hours needed to perform the work
Provide cost estimates to include labor, material and outside services for work orders
Provide up-to-date work load (backlog) status and ensure the accuracy, so that plant wide priorities and use of manpower resources can be optimized
Drive high service level in support of planned and scheduled maintenance work
Work closely with others (Warehouse, Purchasing, Engineering and Vendors) as required in planning and pre-scheduling jobs
Plan jobs and create required job information packages for scheduled work
Prepare and communicate job planning packages for scheduled jobs to all involved and affected
Determine actual sequence of work (i.e. prep work, lock-out, burn and confined space permits required, job steps and necessary follow-up)
Initiate requisitions as needed for planned jobs
Prepare a preliminary weekly schedule for the next work week
Facilitate the weekly scheduling meeting to jointly review/approve the weekly schedule with the Department Managers, Maintenance Manager and Production Planner
Visit job sites to evaluate effectiveness and efficiency audit
Communicate with Department Managers on the status of open work orders and provide feedback on completed work orders.
Demonstrate a working knowledge of company purchasing procedures
Coordinate and follow-up delivery of special equipment needed from vendors
Lead the MRO Materials Team
Exchange common planning information with Planners from other facilities
Provide support by contacting vendors conveying cost and availability of parts
Arrange support personnel, contractors and equipment as needed for the next week’s scheduled jobs
Provide information to update drawings, parts lists, job steps when necessary
Establish and maintain an effective Master Maintenance Schedule for preventative and predictive maintenance activities (PPM)
Day-today operations and management of all store room functions
Manage and train Store Room Attendants
Enforce store room policies and procedures
Input/update asset information in CMMS/EAM system (i.e. vendor information, price, equipment hierarchy, PO#, store room location and any other information that may not have already been captured)
Allocate/reserve stock parts for scheduled jobs in CMMS/EAM system
Manage stock levels needed to support daily manufacturing and maintenance material requirements
Communicate specific requirements to “reserve”, “stage” and “deliver” materials to coincide with scheduled maintenance work.
Qualifications
Qualifications:
Education, Skills and/or Experience Required at Entry:
Skills:
Assertive and influential in coordinating others (in various positions and departments) to provide planning and scheduling related assistance
Comfortable working with managers from all departments
Efficiency minded, well organized and disciplined
High Energy
Results Driven
Organizational design, LEAN and Business planning skills
Communication, interpersonal and problem solving skills
Communication and interpersonal skills
Problem solving skills
Ability to motivate, train and delegate responsibility
Ability to lead, build consensus and work within a team environment
Initiate and manage change
Demonstrate proficiency in Microsoft Office (Excel, Word, Project, Access and Outlook)
Ability to successfully facilitate meetings
Qualifications:
B.S. in mechanical engineering
3+ years relevant experience
Knowledge of plant equipment and processes
Our Social Responsibility platform features a robust, employee-led Give Back program, which includes a matching gifts plan, community grants initiative, and our annual Company-wide Month of Action campaign. With each of these initiatives, our employees are empowered and equipped to give back to their communities and support the non-profits important to them and their families. Through our Give Back program, we own our commitment to Social Responsibility and live our purpose of Packaging a Better Future.
Pactiv Evergreen is committed to a diverse and inclusive workforce. Pactiv Evergreen is an Equal Opportunity Employer. All qualified applicants will receive consideration for employment without regard to race, color, sex (including pregnancy), sexual orientation, religion, creed, age national origin, physical or mental disability, genetic information, gender identity and/or expression, marital status, veteran status or other characteristics or statuses protected by law. For individuals with disabilities who would like to request an accommodation, please call (847) 482-4320 or email TalentHelp@Pactiv.com.
All information will be kept confidential according to EEO guidelines and applicable laws.
#LI-TM1
Job Locations US-FL-Plant City
ID 2023-23557
Category Operations
Position Type Full Time
Pay Type Salaried